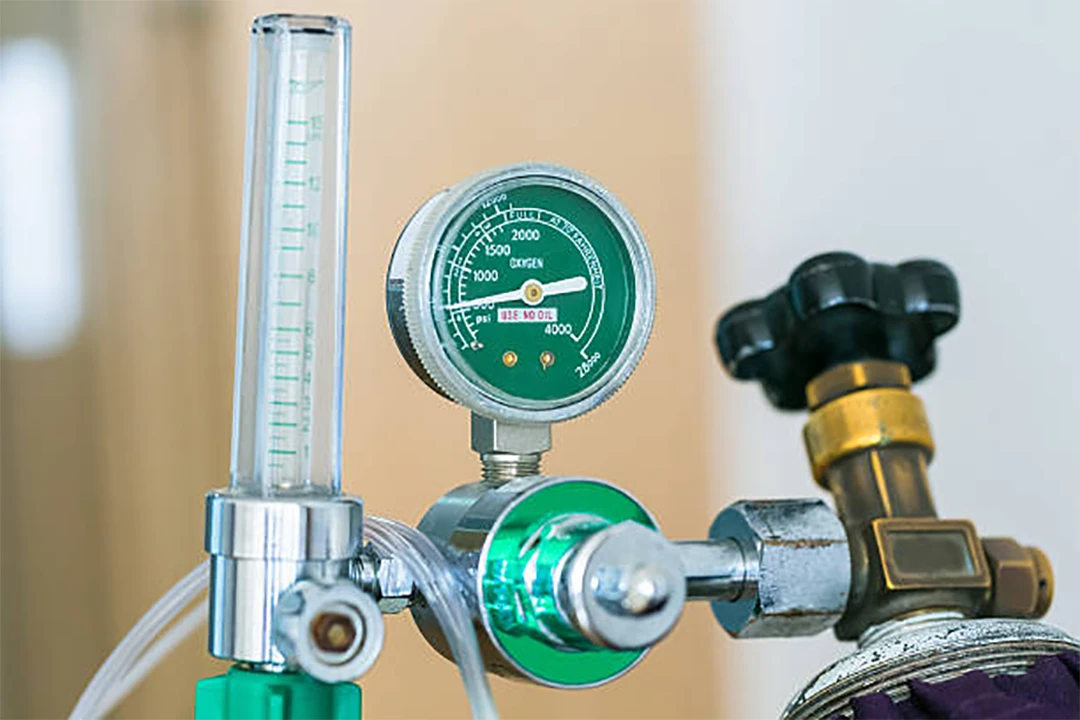
Air regulators are crucial components in various applications, from industrial machinery to medical equipment and even home workshops. They help control air pressure, ensuring optimal performance and safety. Choosing the right air regulator can significantly impact efficiency, cost savings, and operational effectiveness. Here’s a comprehensive guide on what you need to know to buy air regulators.
What is an Air Regulator?
An air regulator is a device used to control and maintain the desired pressure of compressed air in a system. It ensures that the air pressure remains consistent, preventing fluctuations that could damage equipment or lead to inefficiency. Air regulators are commonly used in industrial machinery, medical equipment, automotive applications, and home workshops. They help optimize performance by reducing excessive pressure, protecting sensitive tools, and improving overall efficiency.
When to Use Air Regulators
Air regulators should be used whenever there is a need to control and stabilize air pressure in a system. They are essential in industrial operations, medical applications, and home projects to prevent overpressure damage and ensure equipment efficiency. Use air regulators when operating pneumatic tools, air compressors, or gas distribution systems. They are also necessary for precision-based tasks such as spray painting, laboratory experiments, and food processing. In HVAC systems, they help maintain steady airflow, improving energy efficiency. By using an air regulator, you can enhance safety, protect machinery, and optimize overall system performance.
1. Understand the Purpose of an Air Regulator
An air regulator maintains consistent air pressure within a system, preventing fluctuations that could damage equipment or lead to inefficiency. It ensures that pneumatic tools, air compressors, and industrial processes function effectively by regulating airflow and reducing excessive pressure.
2. Types of Air Regulators
There are different types of air regulators designed for various applications and one should know to buy air regulators:
General-Purpose Regulators: Used in standard air systems to maintain a steady pressure level.
Precision Regulators: Provide highly accurate pressure control, ideal for sensitive applications.
High-Flow Regulators: Designed for systems requiring a larger volume of air.
Piston Regulators: Used for high-pressure applications where a diaphragm regulator may not be effective.
Medical Regulators: Specifically designed for healthcare and oxygen supply applications.
Understanding the type of regulator required for your specific use is crucial for optimal performance.
3. Pressure Range Requirements
Every air regulator has a pressure range within which it operates efficiently. Consider:
Input Pressure: The maximum pressure entering the regulator.
Output Pressure: The regulated pressure delivered to the equipment.
Choosing an air regulator with the correct pressure range ensures that your system functions correctly without overloading or underperforming.
4. Flow Rate Considerations
Flow rate, measured in cubic feet per minute (CFM) or liters per minute (LPM), determines how much air can pass through the regulator. It’s important to match the flow rate of the regulator to the demand of your pneumatic system. A regulator with an insufficient flow rate can restrict airflow, leading to inefficiencies.
5. Material and Build Quality
The material of the air regulator affects its durability and performance. Common materials include:
Brass: Corrosion-resistant and commonly used in general-purpose applications.
Stainless Steel: Ideal for high-pressure and industrial environments where durability is crucial.
Plastic and Aluminum: Lightweight options suitable for less demanding applications.
Choose a regulator made from materials that suit the environmental conditions of your workspace.
6. Port Size and Connection Compatibility
Ensure that the regulator’s port size matches the fittings in your system. Common port sizes include ¼-inch, ½-inch, and 1-inch. Mismatched connections can lead to leaks and inefficiencies.
7. Adjustment Mechanism
Air regulators come with different adjustment mechanisms:
Knob-Adjusted Regulators: Allow easy manual control.
Lockable Regulators: Prevent unintentional pressure changes.
Automatic Regulators: Adjust automatically based on system demands.
The choice depends on how frequently you need to adjust pressure levels and the level of precision required.
8. Filtration and Moisture Control
Some air regulators come with built-in filters and moisture traps to prevent contaminants from entering the system. This is particularly important in applications requiring clean air, such as painting or medical use.
9. Brand and Manufacturer Reputation
Choosing a reputable brand ensures reliability and quality. Look for customer reviews and ratings, and verify if the manufacturer offers warranties and customer support.
10. Cost vs. Performance
While budget considerations are important, opting for the cheapest regulator may lead to frequent replacements and inefficiencies. Investing in a high-quality regulator ensures long-term reliability and better performance.
Usage of Air Regulators
Air regulators are widely used across various industries and applications, ensuring optimal performance and efficiency. Below are some of the primary uses of air regulators:
1. Industrial Applications
In manufacturing and industrial setups, air regulators are used to maintain the required air pressure for pneumatic tools, conveyor systems, and robotic machinery. They help improve production efficiency and prevent equipment damage.
2. Medical Equipment
Hospitals and healthcare facilities rely on air regulators to control oxygen and other gases in medical devices. These regulators ensure that patients receive the correct flow of oxygen and anesthesia gases, making them vital for patient care.
3. Automotive Industry
Air regulators play a crucial role in automotive repair and painting. They help maintain the right air pressure for spray guns, ensuring an even coat of paint without overspray or inconsistencies.
4. HVAC Systems
Heating, ventilation, and air conditioning (HVAC) systems use air regulators to control air pressure and flow, ensuring optimal performance and energy efficiency in homes and commercial buildings.
5. Laboratories and Research Facilities
Scientific laboratories use air regulators in gas chromatography and other analytical instruments. These regulators ensure precise control of gases used in experiments, maintaining accuracy and consistency.
6. Food and Beverage Industry
In food processing plants, air regulators control the pressure in pneumatic systems used for packaging, bottling, and food processing equipment. This helps maintain hygiene and efficiency in production lines.
7. Home and DIY Applications
Home users and hobbyists use air regulators with air compressors for tasks such as inflating tires, operating air-powered tools, and painting. A properly regulated air supply enhances tool performance and safety.
Final Thoughts
Purchasing the right air regulator requires careful evaluation of your system’s requirements, including pressure range, flow rate, material, and compatibility. By considering these factors, you can ensure efficient operation, reduce maintenance costs, and improve overall productivity. Whether for industrial use, medical applications, or home projects, air regulators play a vital role in ensuring consistent and safe air pressure control.